With the rapid development of modern mechanical engineering technology, the requirements for material properties are increasingly stringent, especially under extreme conditions such as high temperature, high speed, strong corrosion, etc., traditional metal materials and polymer materials have been difficult to meet the needs. Silicon nitride (Si ₄) As an advanced ceramic material with excellent overall properties, the silicon nitride balls made of it show their unique characteristics and wide application prospects in the field of mechanical engineering. In this paper, the properties and characteristics of silicon nitride balls are reviewed, their specific applications in mechanical engineering are discussed, and their future development trends are prospected.
Silicon nitride ceramics are known as "the pearl in the crown of advanced ceramics" for their high strength, high hardness, good thermal stability, corrosion resistance, oxidation resistance and self-lubrication. As an important form of silicon nitride ceramics, silicon nitride ball not only inherits the excellent properties of silicon nitride ceramics, but also has unique mechanical properties and wide application potential because of its spherical structure. In the field of mechanical engineering, the application of silicon nitride balls is gradually becoming one of the key technologies to improve equipment performance, extend service life and reduce maintenance costs.
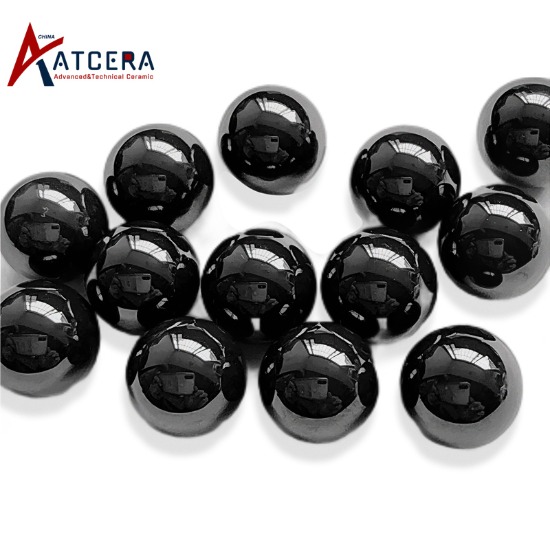
Performance Characteristics of Silicon Nitride Ball
1. High temperature stability
Silicon nitride balls are known for their excellent high temperature stability and are able to maintain their excellent mechanical properties in extremely high temperature environments. This material will neither soften nor melt at high temperatures, making it ideal for bearings, seals and transmission components in high temperature environments. Their excellent thermal stability makes silicon nitride balls excellent in industrial applications that require high temperature loads, such as aerospace and nuclear industries.
2. Excellent wear resistance
The high hardness and self-lubricating properties of the silicon nitride ball give it excellent wear resistance. In friction pairs, silicon nitride balls can significantly reduce wear, thereby extending the service life of the equipment. This characteristic makes the silicon nitride ball particularly suitable for applications under high speed, heavy load and dry friction conditions, such as high-speed bearings and sliding guides. In these applications, silicon nitride balls can effectively reduce the coefficient of friction and improve the operational efficiency and reliability of the equipment.
3. Corrosion and oxidation resistance
Silicon nitride ball has excellent resistance to a variety of acids, bases and oxidizing media. This material can maintain stable performance in harsh chemical environments and is not easy to be corroded or oxidized. Therefore, silicon nitride balls have a wide range of application prospects in chemical, petroleum and other industries, and can be used to make corrosion-resistant pipes, valves, pumps and other key components.
4. Insulation and non-magnetism
Silicon nitride balls are a good electrical insulator and are not magnetic. This characteristic makes the silicon nitride ball have unique application value in the fields of electronics, medical and precision instruments. In the electronics industry, silicon nitride balls can be used to make high-performance electronic components; In the medical field, its biocompatibility and corrosion resistance make it an ideal material for high-end medical products such as artificial joints and dental implants; In the field of precision instruments, the high-precision machinability and non-magnetic characteristics of silicon nitride balls make them an important part of calibration and measurement tools.
5. High precision processing
With the continuous progress of ceramic processing technology, silicon nitride balls have been able to achieve high precision processing. This high-precision processability enables silicon nitride balls to meet the high requirements of precision machinery for dimensional accuracy and surface quality of parts. In the field of precision manufacturing, the high-precision processability of silicon nitride balls has brought a wide range of application opportunities, such as for the manufacture of high-precision bearings, guides, gears and other key components.
Use of Silicon Nitride Ball in Mechanical Engineering Field
1. Bearings and sliding parts
Silicon nitride balls are widely used in high-speed bearings and sliding rails because of their excellent wear resistance and high temperature stability. These components generate a lot of friction and heat at high speeds, and silicon nitride balls can effectively reduce wear and heat accumulation, thereby improving the operating efficiency and reliability of the equipment.
2. Sealing element
In the environment of high pressure, high temperature and corrosive media, traditional sealing materials are often difficult to meet. The silicon nitride ball seal can perform well, effectively prevent media leakage and ensure the safe and stable operation of the equipment. This kind of sealing element has a wide application prospect in chemical industry, petroleum industry, etc.
3. Precision measurement and calibration
The high-precision workability and non-magnetic properties of the silicon nitride ball make it an ideal standard ball or calibration element in precision measuring instruments. During the measurement and calibration process, the silicon nitride ball provides an accurate reference and ensures the accuracy and reliability of the measurement results. This is of great significance for improving product quality and reducing production cost.
4. Medical devices
In the field of medical devices, the biocompatibility and corrosion resistance of silicon nitride balls make them an ideal material for high-end medical products such as artificial joints and dental implants. These medical products need to be implanted into the human body for a long time and in direct contact with human tissues, so the biocompatibility and corrosion resistance of the material is extremely high. Silicon nitride balls are able to meet these requirements and provide safe and reliable medical services to patients.
5. Aerospace and Nuclear industry
In extreme conditions such as the aerospace and nuclear industries, the application of silicon nitride balls shows great potential. Devices in these areas need to withstand extreme conditions such as high temperatures and high radiation, and silicon nitride balls are able to maintain their excellent performance and meet these requirements. Therefore, silicon nitride ball has a wide range of application prospects in key fields such as aircraft engine bearings and nuclear reactor components.
As an important representative of advanced ceramic materials, silicon nitride balls show excellent performance characteristics and wide application prospects in the field of mechanical engineering. With the continuous progress of material science and processing technology, the preparation cost of silicon nitride balls will be further reduced, the processing accuracy and performance will continue to improve, and its application fields will continue to expand. In the future, silicon nitride balls are expected to play a key role in more high-end equipment manufacturing and promote the innovation and development of mechanical engineering technology. At the same time, further study on the relationship between microstructure and properties of silicon nitride spheres and exploration of new composite silicon nitride materials will be an important direction of future research.